The Stantonian, (Magazine of Stanton Ironworks) Vol 22, No.6, April 1961
“In our last issue readers were given a brief account of the floods caused when the Nutbrook stream overflowed its banks on Sunday December 4th last year. The floods were caused by exceptionally heavy rain the previous night and as a result both the Coke Oven and Ore Preparation plants were put out of action.
It was 7am when the first trickle of water flowed into the works and in the centre of the main road serving the Coke Oven plant water soon gathered to a depth of two to three feet outside the Booster House.
By 8am, water was coursing down the road, and it became quite obvious that power supplies to the plant would have to be cut off. In view of this, coke pushing and charging operations well completed and operations at the Coke Oven battery were stopped. To avoid the danger of the ovens becoming overheated the gas supply for heating the battery was shut off at 9:45 am and the steam driven exhausters which serve to draw the crude gas from the battery and to send it through the various units of the byproduct recovery plant were stopped. The gas still being produced from the coal in the ovens was allowed to escape into the atmosphere through the bleeders.
Meanwhile, Coke Oven personnel were endeavouring to prevent the water flooding vital pumping installations below ground level. Dams were hurriedly constructed but, in spite of the strenuous efforts made by everyone on the scene come back the hot well and benzole plant pump houses were flooded to a depth of 10 feet and the boiler basement was completely inundated. At the height of the floods the depth of water at the entrance to the plant was four feet.
The water level began to subside at 2pm and by ten that night it became possible for the Stanton Fire Service to begin pumping out the flooded pump houses. When this operation had been completed, members of the electrical department moved in to carry out an inspection to find that some 60 electric motors had been affected as had switch gear and cables. Unaffected were the motors of the cold-water circulating pumps, and the motors of the quenching water pumps had been made safe by the closing of the drainage sump valve.
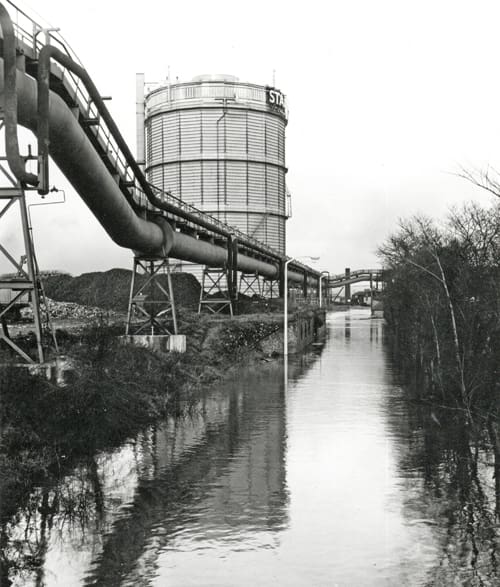
Nevertheless, it was impossible to restart battery operations even on a reduced scale until the hot well pumps, motors and switch gear had been cleared of water. These pumps are used to send water which has become heated in its passage through heated plant over the cooling frame and back into the cold well.
This job was given top priority, and the Stanton Fire Service began pumping out operations with their own pumps augmented by one capable of handling 1000 gallons a minute which was loaned by the Derbyshire Fire Service. With a foot of water left in the hot well pump basement, electricians and fitters began disconnecting the electric motors and brought them out for drying. It was soon realised however that it would take days to dry out the larger motors, even with the considerable facilities available and so began the task of seeking replacements.
It was imperative that the plant should be restarted as soon as possible for the East Midlands Gas Board in spite of having brought all their auxiliary production units into operation were in serious difficulties and had told us that unless a considerable amount of gas was available by Tuesday then supplies to consumers would have to be reduced.
This came as no surprise; for Stanton supplies no less than a quarter of the gas consumed in Nottinghamshire, Derbyshire, Leicestershire and Northamptonshire. No satisfactory replacement motor to drive the hot well pump could be obtained however and so the Stanton Fire Service put two of their own pumps in parallel with two belonging to the Derbyshire Fire Service and these drew water from the hot well. This water was delivered into an adapter which had been contrived and fitted to the hot well pump delivery main by the Coke Oven maintenance department. The total capacity of the four pumps amounted to 1400 gallons a minute and was sufficient to enable the plant to begin operating on a reduced scale. Starting up operations began at 6:50 pm on Monday December 5th and were successfully completed by 11 pm. By 6 am on Tuesday one and a half million cubic feet of gas had been dispatched to the East Midlands Gas Board. The benzol recovery plant was bypassed because the motors were flooded; the benzole left in the gas had the effect of increasing the volume available for sale.
Fortunately, one of the vital hot well pump motors had been dried out by the Tuesday afternoon and the output from the plant was stepped up to supply a further 18,000,000 cubic feet to the gas grid. Working on a system of priority, more motors were dried out and put to work and on Wednesday the full supply of one million cubic feet per hour was restored.
The Ore Preparation Plant was less seriously affected than the Coke Ovens and flooding was confined to the basements and the main chimney flue at the sinter plant. As at the Coke Ovens, electric motors, switches and cables were affected and both the main crusher and the sinter plant were put out of action. The reclaimers were kept going under very difficult operating conditions and production was restored at the sinter plant in about 12 hours. Supplies of iron ore and sinter to the blast furnaces were not seriously affected. The work of pumping out the basements and drying out the electrical equipment took some little time, and the primary crusher was the last unit to come back into operation on the following Wednesday.
That Stanton’s Coke Oven Plant and Ore Preparation Plant were so soon in full production after this major misfortune reflects great credit on all who took part in the restoration of normal working.”
Thanks to Jason Toone for donating this issue of the Stantonian.
Definitions (Wikipedia)
Sinter plants agglomerate iron ore fines (dust) with other fine materials at high temperature, to create a product that can be used in a blast furnace. The final product, a sinter, is a small, irregular nodule of iron mixed with small amounts of other minerals. The process, called sintering, causes the constituent materials to fuse to make a single porous mass with little change in the chemical properties of the ingredients. The purpose of sinter is to be used converting iron into steel.
In the United Kingdom, benzole or benzol is a coal-tar product consisting mainly of benzene and toluene. It was originally used as a “motor spirit”, as were petroleum spirits. Benzole was also blended with petrol and sold as a motor fuel under trade names including “National Benzole Mixture” and “Regent Benzole Mixture”. NB : At this time, British Mains Gas was made from coal – ie ‘Coal Gas’, not the natural gas used since the 1970s.